Your Overview to Comprehensive Welding Inspection Milwaukee Solutions
Just How Welding Evaluation Adds to Durability and Reliability in Fabrication Jobs
Welding assessment serves as a foundational component in guaranteeing the long life and reliability of construction tasks. By systematically determining prospective defects throughout different stages of manufacturing, welding examinations not only protect against pricey failures however additionally foster a society of high quality guarantee within the team.

Value of Welding Inspection
Guaranteeing top quality via welding inspection is an important part of any kind of manufacture project. It acts as a guard to confirm that welding processes fulfill established criteria and specs, thus enhancing the overall honesty of the framework or part being made. Welding examination is not just a step-by-step action; it is an essential practice that helps determine possible concerns early, making certain that they are resolved prior to they intensify into considerable issues.
The significance of welding evaluation can be underscored by its role in keeping safety and security and longevity. Bonded joints are often subjected to extreme problems, and any flaws can jeopardize the performance and longevity of the final product. By applying extensive assessment procedures, organizations can guarantee conformity with market regulations, therefore lessening dangers connected with architectural failures.
Moreover, efficient welding evaluation cultivates confidence amongst stakeholders, consisting of clients and regulative bodies, that the job meets the best standards. This not just enhances the online reputation of the producer yet likewise adds to long-lasting price savings by staying clear of rework and potential responsibilities. Ultimately, welding assessment is integral to the success and dependability of fabrication jobs, enhancing the value of quality control in engineering techniques.
Usual Welding Issues
Welding issues can significantly undermine the architectural honesty of made parts, making their recognition and correction vital. Usual welding flaws can be generally classified into three types: geometric, metallurgical, and service-related.
Geometric defects consist of concerns such as damaging, where the base steel is deteriorated at the side of the weld, and excessive convexity, which can result in tension concentration points. These defects can compromise the toughness and longevity of the weld joint.
Metallurgical problems emerge from inappropriate welding treatments or materials, leading to troubles such as porosity, where gas pockets develop within the weld, and lack of fusion, which takes place when the weld metal fails to bond properly with the base steel. These problems can significantly damage the weld's performance.
Service-related flaws may not come to be obvious until after the part is in usage. Examples consist of splitting due to thermal stress and anxiety or tiredness, which can lead to disastrous failures otherwise addressed.
Recognizing these common issues empowers makers to execute effective assessment strategies that improve the reliability and durability of their tasks, eventually making certain safety and efficiency standards are satisfied.
Examination Methods and methods
A thorough technique to evaluation methods you can try this out and approaches is important for reducing and determining welding issues in fabrication projects. Various methods are used to ensure the stability of welds, consisting of aesthetic evaluation, ultrasonic testing (UT), radiographic screening (RT), magnetic fragment screening (MT), and color penetrant testing (PT) Each method has its strengths and certain applications.
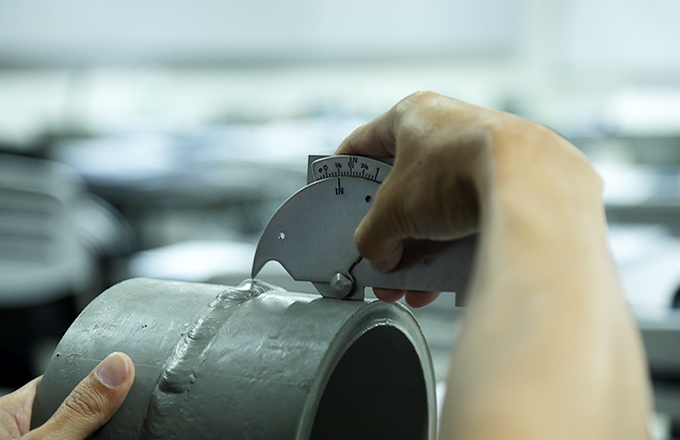
Magnetic particle testing is advantageous for finding surface and near-surface issues in ferromagnetic materials. By using a magnetic field and utilizing ferrous particles, examiners can identify interruptions efficiently. Color penetrant testing highlights surface-breaking flaws via the application of a dye that leaks into splits, making them visible under ultraviolet light.
Utilizing a mix of these approaches ensures a rigorous analysis, boosting the dependability of welded structures.
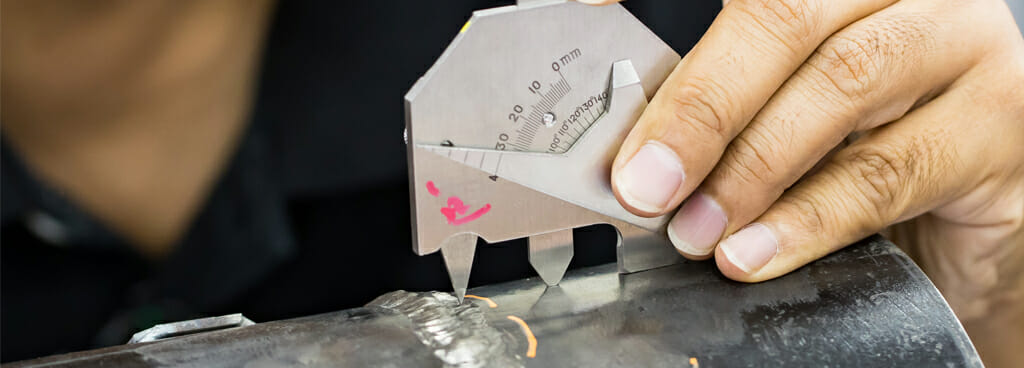
Effect On Task Longevity
Efficient examination practices substantially affect the durability of construction tasks. By determining potential issues and variances in welding processes, inspections guarantee that structures are built to see it here hold up against functional anxieties gradually. When welds are completely examined, the likelihood of unseen concerns, which might lead to architectural failings, is decreased.
Normal assessments help with adherence to industry requirements and policies, which are crucial for making certain the longevity of welded joints. Such compliance not just enhances the honesty of the project yet likewise reassures stakeholders pertaining to the high quality these details of the job. Timely discovery of flaws enables for rehabilitative actions to be taken early, protecting against costly repair work or full overhauls down the line. Welding Inspection Milwaukee.
In addition, efficient examination practices foster a culture of quality control within manufacture teams. They are much more likely to stick to ideal practices and preserve high requirements throughout the manufacturing procedure when employees are aware that their work will be carefully reviewed. Inevitably, this commitment to quality not only prolongs the life-span of the task yet also decreases maintenance prices, thereby improving the general financial stability of manufacture endeavors.
Enhancing Integrity in Fabrication
Integrity in manufacture is dramatically boosted with extensive inspection procedures that resolve prospective weaknesses in welding methods. Efficient welding assessment not only determines issues early yet likewise supplies vital responses to welders, guaranteeing adherence to established standards and specifications. By using non-destructive screening methods, such as radiographic or ultrasonic evaluations, fabricators can ascertain the integrity of welds without endangering the material.
In addition, routine evaluations promote a culture of top quality and responsibility amongst construction teams. When welders comprehend that their work is subject to rigorous analyses, they are most likely to follow finest techniques and methods. This proactive strategy minimizes the danger of costly failings throughout the operational phase of a project.
Ultimately, improving integrity in fabrication through detailed evaluation refines not only raises the life expectancy of the produced parts but likewise strengthens stakeholder self-confidence in the job's general quality and durability. Investing in durable welding inspection methods is essential for attaining long-term integrity in any fabrication venture.
Verdict
In recap, welding examination serves as a crucial element in making sure the longevity and reliability of construction tasks. Eventually, efficient welding evaluation techniques reinforce stakeholder self-confidence and substantially add to the financial practicality of construction endeavors.
Welding inspection offers as a fundamental aspect in making certain the longevity and integrity of construction jobs.Making certain high quality via welding assessment is an essential component of any type of construction task. Ultimately, welding assessment is essential to the success and integrity of manufacture projects, reinforcing the value of high quality guarantee in engineering methods.
A comprehensive method to evaluation techniques and approaches is vital for determining and minimizing welding flaws in fabrication tasks.In recap, welding inspection serves as a vital component in making sure the longevity and reliability of manufacture tasks.